REFERENCES & PARTNERS
Below you will find some of our distribution partners and well-known customers
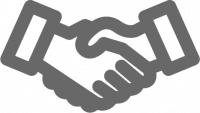
Our goal is a future-oriented partnership and close contact with our customers.
Our Offices & Contractual partner
Are you interested in our products?
Please feel free to contact us directly, we will set up contact with one of our sales partners.
There is no sales partner in your country yet?
No problem, we process your inquiry directly in house.
Mega a.s.
Mega a.s.
Mega a.s.
Mega a.s.
Mega a.s.
Mega a.s.
Mega a.s.
Mega a.s.
Mega a.s.
Mega a.s.
Mega a.s.
Mega a.s.
Mega a.s.
mega a.s.
mega a.s.
mega a.s.
mega a.s.
mega a.s.
mega a.s.
mega a.s.
Wuxi Material Science Engineering Co., Ltd.
Spiraltec Office in the united arab emirates
Rabdan Mall, Entrance No.3
Office No. 101,
Abu Dhabu, UAE
Sales contact:
Mr. Mohammad Hasan (Sales Engineer Middle East)
phone +971 58 960 5588
email
Spiraltec Headquarters - Sachsenheim, Germany
Below you will find some reference customers:
The aim of FYSAM Auto Decorative GmbH was to discharge an aluminium quantity of 1 kg/h from an anodizing bath in order to maintain a desired aluminium concentration permanently in the bath. In order to solve this problem, a module system with 10 spiral membrane modules was integrated into the plant. The volume flow of the spiral membrane modules amounts 15 l/h.
We were commissioned by Grau & Wagenblast with the following key data: Two anodising baths with a filling quantity of 2000 litres each and a desired aluminium discharge quantity of 90 g/h. We realized the project with a compact system of one module, which was integrated into the periphery. This module allows the user to set a variable volume flow ranging from 3 l/h to 15 l/h for the flow through the spiral membrane module. This makes it possible to react flexibly to the amount of aluminium.
The goal of Witte-Metallveredelung GmbH was to process one bath of anodizing. We realized the project with a compact 1 unit system. This system allows the user to set a variable volume flow of 7 l/h to 15 l/h for the flow through the spiral membrane module. This gives the possibility to react flexibly to the amount of aluminum introduced.
At Gretsch-Unitas, a complete system consisting of a DDSU150 supply unit with two DS10 module systems with a total of 15 spiral membrane modules was installed. This system is designed for applications > 100 l/h acidic process solution. Our system was connected to several anodizing baths and operated continuously in three-shift operation.
At ALOXAN we delivered a complete system consisting of a supply unit DDSU150, a module system DS10 with three spirale membrane modules WD-AR10-1001 to prepare an ELOXAL bath of 14 m³. The system was designed to process a volume flow of 50 l/h for a working time of 16 h/day. The customer achieved a sulfuric acid recovery rate of at least 75 %. The sulphate load in the wastewater is reduced, the use of caustic soda for neutralization and the formation of sludge are reduced.
A 72 m³ anodized pool is to be processed at the BWB Group in Switzerland. A complete system with pre-filtering, power supply unit and two module boxes for a total of 14 spiral membrane modules was required to implement this project. The system allows the user to keep the Al concentration target at 9 g/l. The total performance of the volume flow is 120 l/h.
The aluminium input into the anodizing plant at Aalberts Surface Technologies is approx. 0.5 kg/h. The targeted Al concentration in the anodizing bath is 8 g/l. This was achieved with a system consisting of a safety filtration unit, a DDSU150 supply unit and a DS10 module system equipped with 7 membrane spiral modules. The system runs in two-shift operation.
In a second step, the pickling line was equipped with a compact system from the DDP2 series to recover the free hydrochloric acid.
At AMI BV from the Netherlands, two anodizing tanks, each with 4.2 m³, were to be processed. With a metal input of approx. 380 g/h, the feed volume flow to be processed was 40 l/h. A compact system DDP2-01 including a 3-stage emergency filtration and 2 modules of the AR20 series was used. With an operating time of 9 hours per day, a target concentration in the bath of the desired 10 g/l aluminum salt could be maintained.